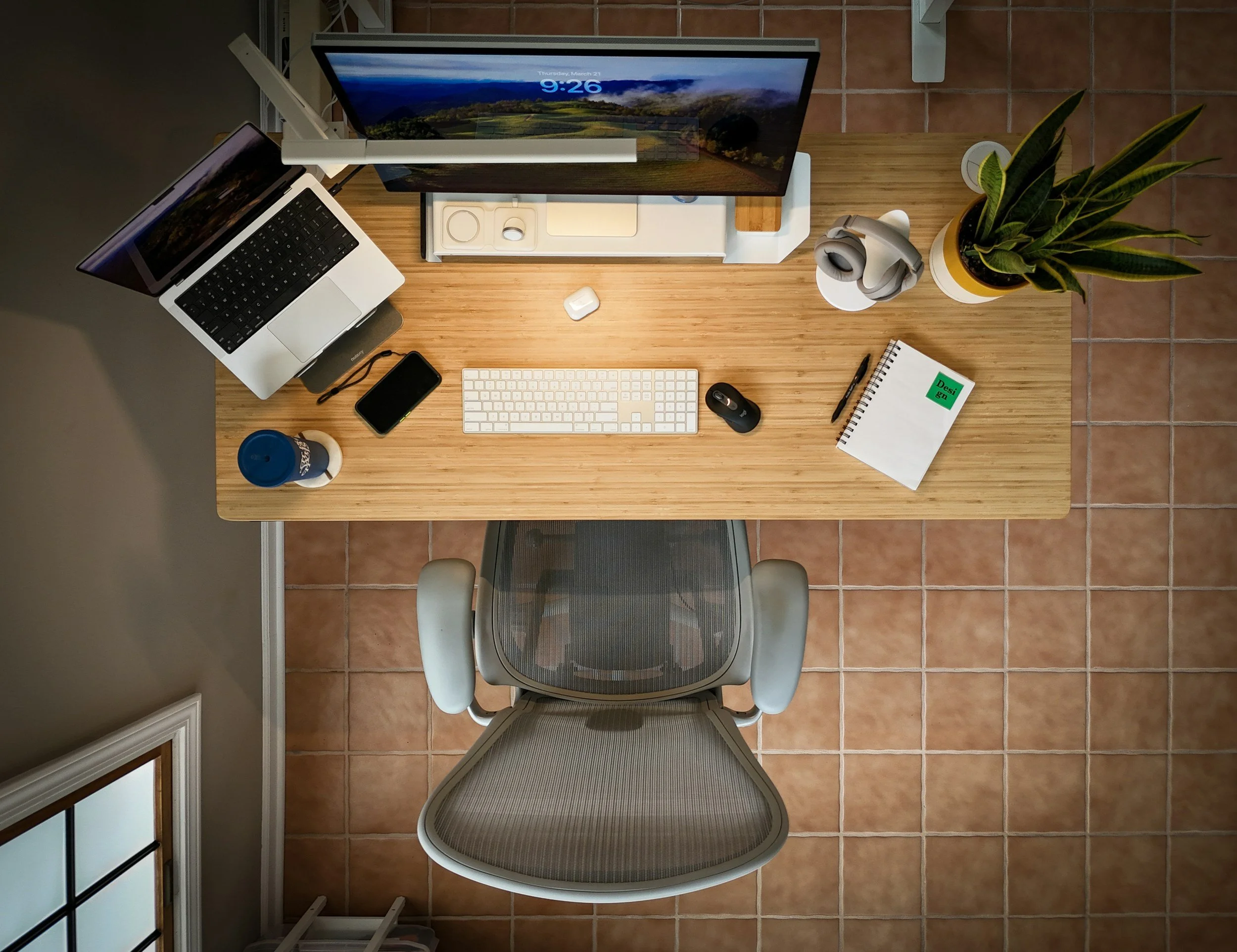
One Month FREE Trial!
The Lean Challenge Community
A New Method of Learning Lean
We Invite You to Join Our Lean Challenge Community
Reduce Costs and Improve Productivity
Improve Quality and Reduce Safety Incidences.
This is not an Event but a Transformation in the Way work is Done.
Don’t guess your way through Lean!
Join us not for a course but for a complete “Lean” journey.
Guided each step of the journey by one of our Lean Coaches
One Month FREE Trial!
A Four Step Method to Reach Your Lean Goals
Step:1
Learn Lean Basics & Identify areas to improve your work area.
Identifying Improvement Areas
The Diagnostic Approach to Lean Manufacturing
Imagine walking into a workplace as a lean manufacturing consultant—much like a therapist entering a patient's first therapy session. There's an intuitive sense that something isn't quite right, but pinpointing the exact issue requires careful observation, analysis, and understanding.
Recognizing the Underlying Challenges
Many organizations experience a persistent feeling of inefficiency. You might recognize symptoms such as:
Consistently high production costs
Low productivity rates
Frequent bottlenecks in processes
Unexplained waste
Employee frustration
Inconsistent quality outputs
These are signals that something in your work area needs improvement, but the solution isn't always immediately apparent.
Phase 1: Identify a Problem or Problem Area
Step 2:
Learn Lean Concepts, Principles and Practices.
Learn about Lean and the benefits Lean has to offer.
In the Lean Challenge, you will learn about Lean and then try out what you learn.
You will also receive FREE weekly Lean coaching sessions
Step 3: Use Lean Tools to Solve Your Problem.
A while ago, we were doing a Lean presentation to upper management in a large grocery chain.
A small team from the deli was presenting their Lean activity.
When it was time for one of the deli workers to present his problem, he simply brought into the front of the room a cart with a beautiful 20 lb. roast beef on the top shelf.
And then, in his own way of presenting his problem, he picked up the roast in front of the upper management and threw the beautiful piece of meet into the garbage can!
And then he simply turned to the audience and said, “We throw that much roast beef away each night. And that is my problem!”
There was a brief silence in the room as people processed what they had just seen!
Lean can be that simple.
It’s obvious to you that there is a problem.
When you are taught Lean tools, you will learn how to eliminate the problem.
Step 4 - Set New Standards
Clients often tell us that they have had a special Lean training or even a five day Lean event.
But in a very short time, the improvements returned to the way they were.
During the Lean Challenge, consisting of 4-three month quarters, you will learn a method to sustain your improvements.
Enroll In The Lean Challenge Community Here
Affordable Pricing
Students move through the training at their own pace
$275 per month
FREE weekly online Lean Coaching.
Additional 1:1 Lean Coaching Calls are available for purchase as needed.
One Month Free Trial!
Register Here For The Lean Challenge!
LET’S GET GOING!
LEAN BLOGS
A Few Of Our Clients
Hello, and welcome to The Lean Learning Academy!
My name is Ben Root and I am a senior coach with The Academy.
My journey in training and development began at Kent State University, where I earned a Bachelor’s Degree in Business Administration.
While working at NUMMI I received a Master’s Degree in Human Resource Development from Golden Gate University in San Francisco, CA.
The real excitement for developing others sparked when I joined NUMMI.
There, I had the unique opportunity to watch first hand as an automobile company with over 7,000 employees went from the Worst of the Worst automobile plants in the world to the Best of the Best plants in a very short time.
The backbone of this transition was the Toyota Production System or what many today call “LEAN”.
Ben Root The Lean Learning Academy